Developing quieter propellers for electric powered flight
Aachen, Germany – July 4, 2025
Helix Propellers is proud to announce its participation in a groundbreaking new research project—FlüsterProp.NRW (“WhisperProp.NRW”)—a state-funded initiative dedicated to advancing quiet, sustainable aviation. This collaborative effort, supported under the Luftfahrt.NRW funding guidelines by the Ministry for the Environment, Nature Conservation and Transport of North Rhine-Westphalia, aims to develop a low-noise, lightweight carbon fiber propeller for electrically powered training aircraft. The project officially kicked off today at FH Aachen’s Department of Aerospace Engineering with a formal award ceremony.
During the event, State Secretary Viktor Haase presented the official funding decisions on behalf of the North Rhine-Westphalian government. Addressing the project partners and invited guests, Haase emphasized the urgent need to reduce aircraft noise, particularly in densely populated regions. “Aircraft noise is a burden for many citizens. The state of North Rhine-Westphalia is addressing this issue and is committed to innovative and quiet aviation,” he said. “That’s why we are supporting technologies that actively reduce noise pollution—such as low-noise propellers for electric aircraft.”
The total fundi
ng for the project amounts to approximately €900,000, with Helix Propellers receiving support to carry out key stages in development, manufacturing, and experimental validation.
A Vision for Quiet, Climate-Friendly Flight
Electric aircraft represent a significant step toward a greener future in aviation, yet they are not inherently silent. Although electric motors drastically reduce overall noise levels compared to internal combustion engines, the propeller remains the dominant source of sound during flight—especially during high-power phases like takeoff and climb. This is where FlüsterProp.NRW comes in.
The project, a joint effort between:
FH Aachen University of Applied Sciences (project lead)
Helix-Carbon GmbH (manufacturing and design)
Westflug Aachen Luftfahrtgesellschaft GmbH & Co. KG (aircraft operations and maintenance)
seeks to design, build, and test an innovative “whisper propeller” for electric aircraft, with the primary test platform being the Pipistrel Velis Electro. The target: a noise reduction of at least 3 dB(A)—enough to make the aircraft indistinguishable from background noise in urban airspace. That degree of noise reduction represents a breakthrough in low-impact air mobility and paves the way for broader adoption of electric flight near residential areas.
The Road to a Flight-Ready Prototype
The FlüsterProp project spans three years and is broken down into three major work packages:
1. Holistic Propeller Optimization
The first phase focuses on defining a detailed technical and regulatory requirements profile for the propeller. FH Aachen and Helix will collaborate to optimize the propeller using a multi-disciplinary simulation approach—aerodynamics, aeroacoustics, structure, aeroelasticity, and manufacturability are all modeled and refined in tandem.
Key to this process is the use of “PropCODE,” a proprietary optimization software developed by FH Aachen in partnership with Helix. High-fidelity simulations will be run using Simcenter STAR-CCM+ and validated through both experimental and numerical methods.
To ground the optimization in real-world data, FH Aachen will use 3D scanning, in-flight noise measurements, and comparative testing of existing propellers on the NEFT project aircraft, which have been operating since 2021 as electric training platforms.
2. Manufacturing and Integration
Once the design is finalized, Helix will begin production of the whisper propeller, leveraging its extensive experience in advanced carbon fiber reinforced plastic (CFRP) composites. One of the engineering goals is to reduce the propeller’s mass by up to 2 kilograms, further improving aircraft efficiency.
The propeller will be fabricated, integrated into the Pipistrel Velis Electro, and rigorously tested on the ground to obtain a Permit-to-Fly (PtF). These ground tests include structural fatigue and fracture testing, dynamic analysis, and safety verification using both finite element (FEM) and CFD simulations.
3. Flight Testing and Performance Validation
With the PtF granted, the project moves to full-scale flight trials. These tests—scheduled for weather-favorable months—will evaluate both noise emission and aircraft performance under real operating conditions. The aim is not just to reduce decibels, but to verify that flight safety, handling, and maintenance demands remain within practical and regulatory limits.
Noise tests will be performed according to ICAO Annex 16 standards, using FH Aachen’s certified noise measurement systems, which will be upgraded with a new acoustic camera for greater accuracy.
Beyond the Propeller: Broader Impact and Future Applications
While the FlüsterProp is initially aimed at electric aircraft, its success could influence noise reduction strategies across general aviation—including kerosene-powered aircraft, where quieter operation and improved fuel efficiency are always in demand.
Additionally, the project will explore recuperative energy strategies—the ability of electric aircraft to regenerate energy during descent or gliding. This requires unique propeller characteristics that are also being taken into account during development.
As Prof. Dr.-Ing. Frank Janser, project leader at FH Aachen, explained: “The crucial thing is that we can test in real operation at the Aachen-Merzbrück research airfield. This allows us to validate our design under real-world conditions, not just in simulation.”
Students will also be directly involved in the project through thesis work, internships, and research assistant roles—further strengthening the integration of academia and industry in North Rhine-Westphalia.
Helix Propellers’ Role
For Helix, the project builds on a legacy of pushing innovation in carbon composite propellers for light and ultralight aircraft. As the lead for manufacturing and integration, Helix will:
Manage the fabrication of all propeller prototypes
Guide the design to meet practical constraints of cost, durability, and manufacturability
Operate a specially modified acoustic test bench to validate noise emissions before flight testing
The company’s involvement doesn’t end with this project. The long-term vision is to launch a family of certified whisper propellers adaptable to multiple aircraft types—creating both environmental and economic value.
A Step Toward a Quieter Aviation Future
With air mobility poised to become more sustainable and localized, noise becomes a defining factor in public acceptance. FlüsterProp.NRW directly addresses that challenge with cutting-edge engineering, regional cooperation, and real-world testing.
By 2028, the project aims to deliver a fully validated, flight-ready low-noise propeller, with noise reduction targets met and the groundwork laid for broader market application.
Helix Propellers is proud to help lead this transformation—where innovation meets sustainability, and quiet skies are no longer just a dream.
Learn more about the event from FH Aachen (in German): FH Aachen Newsroom Article
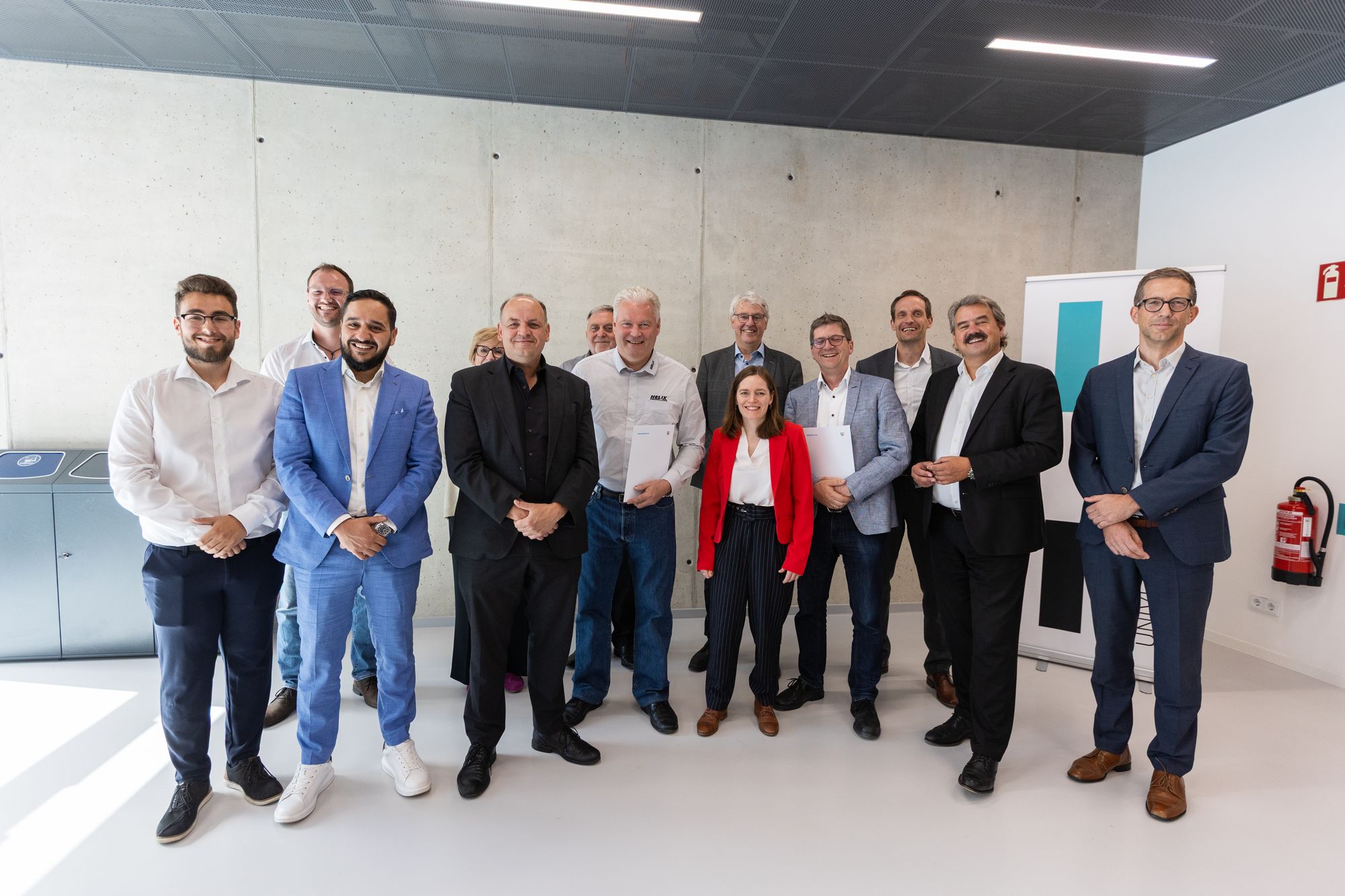